Why Reinvent the Wheel? Ford Returns to In-house Operations to Compete with Tesla for Top Electric Vehicle Manufacturer
When discussing the topic of Electric Vehicles, a singular company comes to mind. Since 2008, Tesla has made a name for itself for being the go-to EV manufacturer, with legacy automotive companies paling in comparison.
Yet, the initial trailblazing automotive marque, Ford, is positioning itself with aspirations to reclaim its authoritative legacy in the automotive realm and take the EV crown from Tesla – at least, that’s the vision outlined by Ford’s CEO, Jim Farley.
Rocky Start for Ford
As of now, this mission hasn’t been actualized. Ford’s initial plans for EVs set in 2022, haven’t met its progress projections. Ford’s CEO, Jim Farley, even stated that the company could have generated an additional $2 billion.
“We should have done much better last year. We left about $2 billion in profits on the table that were within our control, and we’re going to correct that with improved execution and performance.”
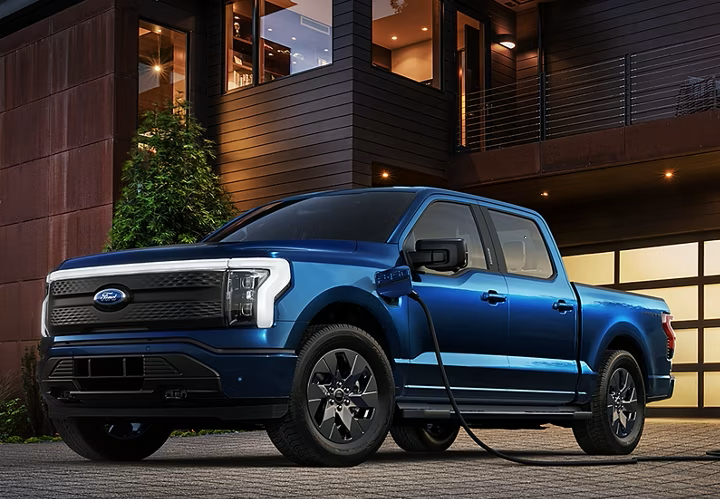
Ford F-150 Lightning
2023 also started with a challenge for Ford. Ford’s debut electric truck, the F-150 Lightning, was in the design phase and faced a setback. One of the F-150 prototypes caught fire due to a battery pack problem, derailing Ford’s momentum. This incident might trigger a sense of déjà vu for automotive enthusiasts; reminiscent of 2013 when a Tesla Model S sedan also ignited due to an issue with its battery pack design.
Perhaps Ford took some solace in the realization that the EV forerunner, Tesla faced similar challenges with its EV development. Ford recommenced production of the F-150 Lightning a month after the incident.
Problem with Legacy Manufacturers in EV Development
The problem that Ford and other legacy manufacturers face with EV development is not the quality of its products or engineers but its building processes. Like most, Ford outsources its modules in the supply chain to different companies through bidding competition. The idea behind this competition is that it is meant to serve as a way to optimize time and cost savings in developing its vehicles. With an estimated 150 modules in each car, there can be 150 different teams of software developers working on these vehicles.
During a recent installment of the Fully Charged Podcast hosted by Robert Llewellyn, Farley revealed the long-term implications of this approach. According to Farley, each contracted company employs distinct programming languages and varied programming logic, inhibiting the software to operate together – becoming more financially burdensome.
Farley admits that his team at Ford does not understand the software running in the vehicles. Even if they did, Farley says it is not just a matter of updating the language and logic so these different software work together but also has implications on intellectual property (IP) ownership. Despite Ford’s name being on the vehicles the software is in, Ford may not have the legal right to update the software– it is still the software developer’s IP. And it is not as simple as asking the software developers to make modifications. This rework takes time and effort; further delaying the project.
The real problem is the lack of cohesiveness, communication, and one source of truth between the software developers throughout the design process. Without these during software development, the resulting products often suffer from inefficiencies, inconsistencies, and compatibility issues that could have been preemptively addressed.
Tesla’s Design Process
Though they may be competitors, Farley gave credit to Tesla, sharing that what makes the EV manufacturer stand out from others is their design process.
Unlike the legacy manufacturers who outsource their software, Tesla’s design process is entirely in-house. From the requirements stage to the build stage, Tesla employees have a hand in product development from start to finish. This not only grants Tesla full authority over the software but also fosters an environment where software designers can engage in effective communication and collaborate throughout production.
The reason other automotive manufacturers have refrained from emulating Tesla’s approach is the perception that internal operations incur higher expenses compared to the bidding approach. Establishing in-house operations means hiring more staff and buying more equipment to make these developments possible. While this might initially appear as a more substantial upfront investment, it has enabled Tesla to achieve long-term cost savings. This is evident in the company’s ability to avoid release delays caused by flawed prototypes and costly rework.
Future for Ford
In order to preserve jobs and remain competitive, Farley said that Ford will be shifting to in-house operations for its EVs. While other legacy manufacturers will continue to outsource – Ford will begin designing the electrical architecture.
“I watch way too many companies continue to try,” Farley shares. “It is shocking to me to see how many people are sticking with very old electric architectures and software from other people that will never work. And no matter how many software engineers they hire, their car is not going to work. You’re going to have problems. So, we have just decided to insource it all.”
Ford recognizes that the contenders in the EV arena aren’t the conventional players. This is because those automotive manufacturers are grappling with the same obstacles as Ford. Rather than vying with them, Ford is inclined to draw inspiration from manufacturers like Tesla.
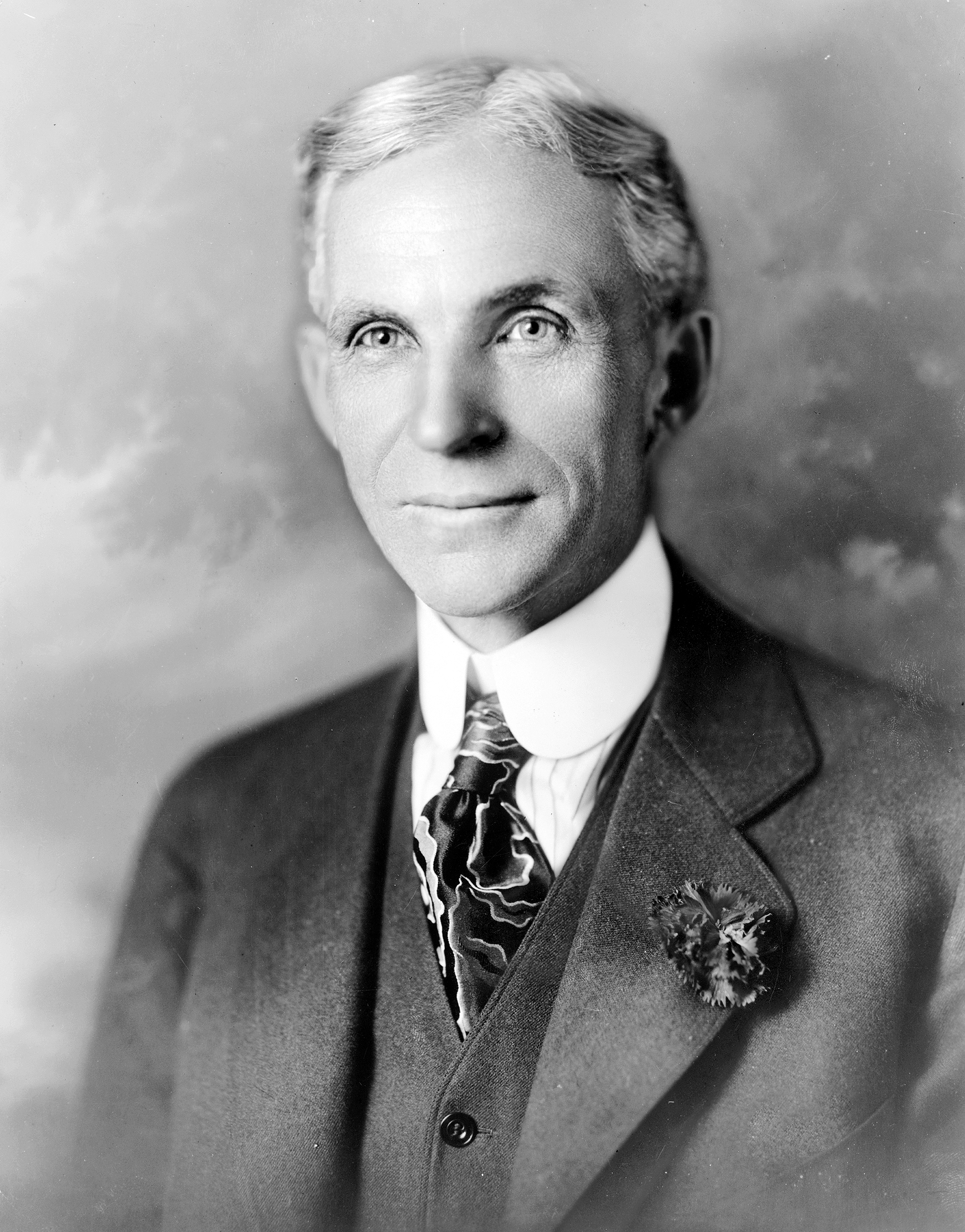
Henry Ford, Founder of Ford
This inward strategy for Ford isn’t an innovation; rather, it’s a revisitation of the original company ethos. To rival the leader, do what you did when you were the leader. Henry Ford’s principles emphasized efficiency and affordability, while his pioneering design decisions influenced the automotive sector. Through standardized components and processes, Ford surged ahead in production compared to its competitors.
“It’s in [Ford’s] DNA.” Robert Llewellyn shared this on his podcast. “The [materials] go into one end of the factory, and then a car comes out the other. That is effectively what Henry Ford did.”
However, the automotive industry is not the same as when Henry Ford first founded the company. Llewellyn noted the challenge for automotive manufacturers is that the technology we put into vehicles today has evolved significantly in recent years; making it nearly impossible for these organizations to rely on its old processes to achieve the desired results. Vehicles contain more lines of code than ever — 100 million lines of code, in comparison, a Boeing 787 Dreamliner only has 14 million.
To fill this knowledge gap, Ford has started to attract and hire new talent to focus solely on software development.
“To do that you need to write all the software yourself. But car companies haven’t written software like this, ever. We’re literally writing the software to operate the vehicle for the first time ever.”
Farley noted that Ford’s current employees should not be apprehensive about job security. The company needs a blend of fresh talents capable of conceptualizing and comprehending the evolving technologies crucial for EVs, along with experienced automotive engineers possessing insights into how the software should function in vehicles.
“You can get the best software person from Apple, but they don’t know anything about safety-critical systems. You don’t want to fire an airbag off the cloud….so you need a mix of traditional people, but you’ve got to make that decision.”
Building a Foundation
Ford is embarking on an extensive endeavor, one that involves constructing and maintaining an innovative software development process. And, this undertaking extends beyond writing code.
In this intricate time that Ford navigates, software requirements emerge as integral components. Their influence on project success cannot be understated, despite their inconspicuous nature. Unseen orchestrators of project fate, requirements have a critical impact on the return on investment (ROI) equation—a matter of paramount concern for Ford. To ensure the viability of its EV lineup as a sustainable corporate asset, maximizing ROI becomes imperative to prioritize.
In the past, requirements served as a method for Ford to communicate with third parties about its cars’ necessities. Which, as Farley has pointed out, wasn’t necessarily accomplished with success.
With this inward shift, requirements function as a channel for internal communication. Insufficient requirements now translate to ineffective internal communication, resulting in wasted time, resources, and internal conflicts. Any of these factors can potentially lead to the downfall of a company, regardless of whether it’s a well-established enterprise or an eager start-up.
But here lies a great opportunity. Ford stands at the cusp of a remarkable advantage. With a reimagined approach and the potential for adept execution, they possess the capacity to forge a software development process that catapults them ahead of rivals. Ford has resources, a time-honored reputation, and a wealth of skilled engineers. The company’s path to success hinges on deliberate and strategic implementation.
Tesla and Ford: Frenemies
Ford’s in-house focus does not mean that outsourcing software is entirely out of the question for Ford. In fact, earlier this year, Ford announced an agreement with Tesla that will provide Ford customers with port access to Tesla’s V3 superchargers across Canada and the United States. This Tesla-developed adapter will be available for Ford’s F-150 Lightning, Mustang Mach-E, and E-transit vehicles.
“Tesla has led the industry in creating a large, reliable, and efficient charging system and we are pleased to be able to join forces in a way that benefits customers and overall EV adoption,” said Ford Model Chief Customer Officer, Marin Gjaja. “The Tesla Supercharger network has excellent reliability and the NACS plug is smaller and lighter. Overall, this provides a superior experience for customers.”
However, this agreement does not mean that Ford and Tesla have the same vision for its EVs.
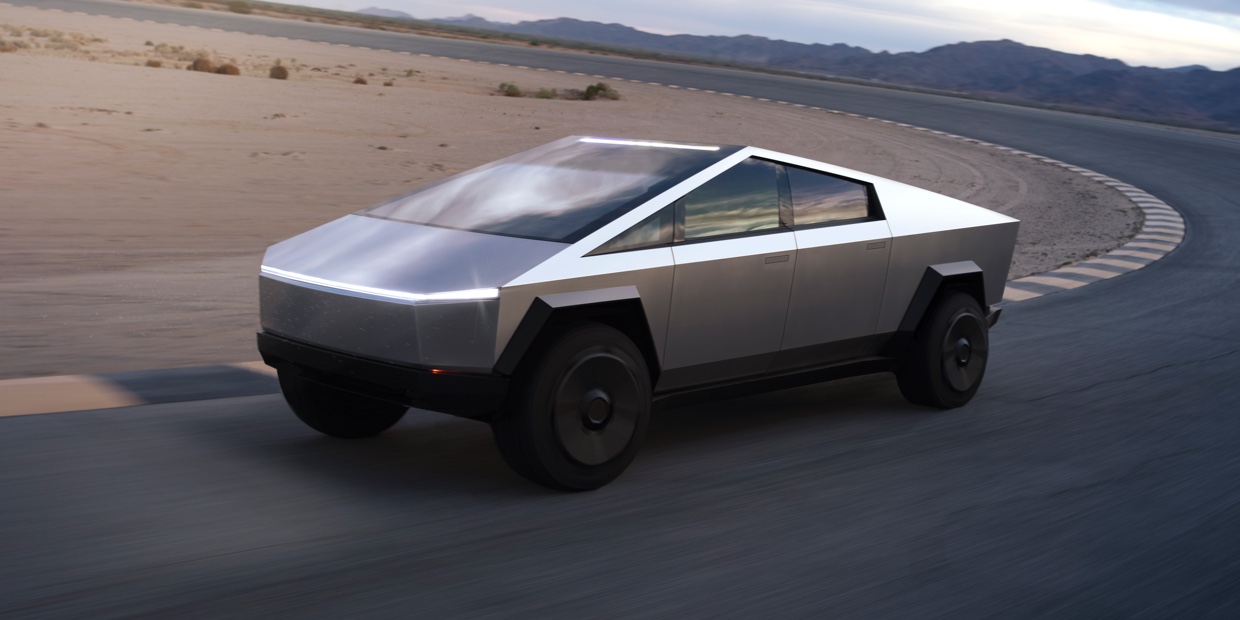
Tesla’s Cybertruck
Following a recovery from the F-150 Lightning setback, Ford faces another challenge as Tesla introduced its inaugural pickup truck, the Cybertruck.
Farley said he is not threatened by Tesla’s newest vehicle, and while the Cybertruck is “a cool high-end product” Ford “make[s] trucks for real people who do real work, and that’s a different kind of truck” – ‘Built Ford Proud.’
Lessons Learned
The process of managing requirements presents a challenge that most organizations encounter, requiring continued efforts to achieve excellence.
Ford faces a substantial pursuit as it navigates the transition. A pivotal factor entails establishing the correct workflows for its software requirements. Given the scale of Ford’s operations, striking the right balance between speed and precision will be crucial in effectively rolling out this approach. Innovative organizational strategies are fantastic until they fail to fulfill stakeholder expectations.
Farley shared that Ford is approaching its EV division with a start-up mentality. The company has been reorganized into three segments, with the EV section being the newest and most immature. This entails adopting novel processes and product strategies while ensuring that Ford’s legacy in the automotive industry doesn’t inflate its sense of competence. The division is fundamentally constructing its foundation, and this involves encountering the same risks typical of most start-up ventures.
If successful, Ford will be responsible for the lifecycle of their requirements, an aspect that has been absent for years. Oversight of these requirements not only grants flexibility throughout development but also fosters enhanced collaboration and more efficient communication across teams. Different teams need to understand how the various components of the vehicles must synergize based on these requirements.
Operating as a start-up within a well-established household brand and moving a significant portion of its operations in-house might appear to be a substantial undertaking. However, it is a risk well worth the reward. These planned changes are expected to serve as the driving force that propels Ford back to leaders in an industry it shaped more than a century ago.
Farley’s vision will streamline production, yielding substantial long-term cost savings. This move will grant Ford autonomy from external contracts, full ownership of its IP, and the capability to standardize operations. By acknowledging the constraints within the existing approach and drawing inspiration from past successes, this decision is set to significantly enhance efficiency, trim production timelines, avoid later-stage errors, and render Ford’s EVs accessible to its target market: ‘real people who do real work.’
Developing your own requirements and looking how you can optimize the process? Try QVscribe.