How to Build with Confidence in MedTech: The 5 Stages of Global Design and Development Guide and Checklist
EXECUTIVE SUMMARY
With the rapidly accelerating pace of innovation in the medical device arena, the procedures and practices of the past are struggling to keep up. As a result, medical device recalls are on the rise, regulatory agencies are implementing increasingly strict controls, and medical device manufacturers are trying to adapt. There are proven methods to reduce risk and improve quality, but the amount of time and effort required to maintain these systems has become burdensome as the functionality and interoperability of devices continue to grow.
The standard Global Design and Development Model is a proven way to reduce risk and maintain quality. This model is based upon the FDA Quality System Regulation (QSR) and ISO 13485. Due to the complexity of new innovations, traditional approaches to these systems are being pushed to their limits. For example, maintaining compliance and quality for a simple product with 500 requirements is a much different endeavor than trying to follow the same procedures for a modern smart device with 20,000 requirements.
Fortunately, as medical device technology has advanced, so have the tools that can offset these risks and facilitate product development. eQMS systems keep you on top of your regulatory requirements and quality systems. Requirement management tools allow you to trace, organize, and reuse your requirements in different projects. And now,
requirement quality tools like QVscribe are here to supercharge development models by automating tedious checks that can be difficult to maintain, but are too important to ignore.
In this guide, we’ll provide a step-by-step process for defining product requirements at each of the 5 major stages in the Global Design and Development model. There will be a particular focus on how to leverage the design input stage to accelerate development and reduce risk with the use of modern tools. We’ll also present each of the 23 must-haves in that section. They can also be found in the form of a checklist at the end of this document.
Stage 1: User Needs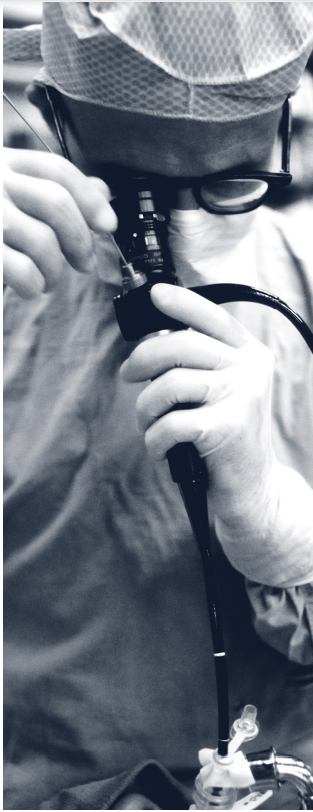
Once an opportunity for a new product has been identified, the first step is to consult with potential users, patients, subject matter experts, and other key stakeholders to get a clear understanding of what user needs the product must meet. These will be used to communicate the user needs to all stakeholders and to establish the high-level acceptance criteria.
Determine the Use Case in the form of a narrative. This is typically handled by a subset of your project team. Best practice is to use a team of three that includes marketing and engineering, so you have various perspectives and get a comprehensive narration. The goal is to identify all the different ways and environments in which your product could be used in order to get as clear of a view as possible on the problems your product will solve.
Translate the use case Narrative into distinct user needs. This is where your requirements start to take shape. user needs are more formalized than the use cases, and each should be unique, structured, and singular in purpose. Every requirement in the next stage will trace back to at least one specific user need. You will uncover additional user needs as you iterate on the requirements, but it’s important to cover as much ground as possible before moving on to the next step. If you can imagine a product that satisfies all your documented user needs, but doesn’t align with the vision for your product, keep going until it does.
In the broader sense, this step is a part of “Requirement Elicitation” or “Requirement
Gathering”. For more on this topic, please see our Requirement Elicitation Technique guide.
Stage 2: Design Input
In this stage, you will develop a complete consistent set of requirements that ensures the device will be fit for the purpose that was defined in Stage 1. Think of your design input as a series of walls that define the general shape of your device – the final design can take on any form, so long as it fits within the confines of the design input.
Translate user needs into design requirements. The centerpiece of this stage is the Product Requirements Document, which is the complete list of all product requirements. The FDA breaks these down into 3 distinct categories, pictured to the right, and we’ve identified 23 different types of must-have requirements to consider across these three categories. Let’s take a look at each one:
Functional Requirements
1. Physical characteristics and exterior design: Document the minimum and maximum size dimensions, and weight of the instrument. Will an operator need to move a module? Is there a shelf space or floor footprint maximum that needs to be met? Make sure your weight and dimensional requirements reflect that.
2. Features and functions supporting user needs and intended use: What’s required for the user to interface with the machine? Determine and document any aspect of the system configuration and sub-system configurations, including disposables and
cartridges that the user will interact with, to ensure that the device’s intended use is met.
3. Software Requirements: For complex devices, this can quickly become the largest set of requirements for the product. You need to clearly define how you want the product to behave under each specific circumstance it may encounter. Computers don’t make decisions, they only do exactly as they’re told, so it’s important to clearly document each of these behaviours so you don’t end up with any avoidable surprises in testing or when the product is in market. The requirements rules defined by the International Council of Systems Engineering (INCOSE) are particularly helpful when defining system behaviors, but they have their limits. More on that later.
4. Product and data security: How will your system retain log files and generate reports? Determine how long that information will be retained and how it can be accessed.
5. Packaging: What kind of packaging is needed for sending, protecting, maintaining sterility, and presenting the product to the customer? Are there other accessory components that are specifically for maintaining product integrity, form, etc. (a mandrel or stylet to maintain a lumen or keep a component straight, for example), that need to be included with the packaging?
6. Labeling and product documentation: Where does product information need to be visible and how will it be read when stored on the shelf? Note which languages the labels need to be, and indicate what user documentation will be included with the instrument and how the language will be determined. Will any of your labeling be in electronic format?
7. Single versus multi-use: Don’t take this for granted. It is important to make sure everyone is on the same page with the number of times each unit, or each specific component, will be used, as this will shape virtually every other design decision. For example, if it is single patient use, is it multi-use within the patient’s procedure? Establishing and clearly communicating this as a numeric value or range as early as possible will reduce the risk of misunderstanding and avoidable rework.
8. Sterile, non-sterile, cleaning: Will the product be offered sterile? If so, what method of sterilization is required? Or instead, does this product need to be sterilized before use? If it’s multi-use, how and with what cleaning agents must it be cleaned and stored?